Fitting an Overdrive Part Two

Linda brought the 4.30:1 gears back to the UK with her and I picked them up from her at the Easter weekend. It took me a day to rebuild the diff with the new gears. It is hard physical work by yourself with few tools.
The next job was to remove the axle housing from the car and cut off the spring mounts so that I could set the pinion at the new angle on the new mounts you see in the photo.
I also fitted a drain plug at this stage.
The brakes I left connected to save having to bleed them!
The axle was then re-fitted with the diff in place so that the pinion angle could be measured. But first the axle has to be centered under the car.
I did this first by measuring from the end of each axle to the springs.
But then I found it was not centered under the body! (Well this is a Dodge!)
So I then set it so that it was right with the bodywork. There was only a couple of mm between the two measurements.
It was then just a matter of setting the pinion to the same angle as the engine/trans.
The theory goes like this;
The center line of the crankshaft and transmission output shaft must be parallel to the center line of the pinion shaft as shown in Figure 1.
You will note that there is some distance between these parallel lines. The distance is caused by the angle of the components and their distance apart.
Planning these component angles is critical. You have to set the components up so their center lines are parallel and so that the angle made THROUGH the U-joints is 3-degrees or less as shown in Figure 2.
While it is possible to run at zero degrees through the U-joints, something more than one degree and less than three degrees seems to run smoothest.
This is something i got very wrong the last time I did it and the car has had a bad vibration since.
I will fit the driveshaft at the weekend and check all the angles again. I should have 1.5-2 degrees at the drivshaft when it is in. If I need more driveshaft angle I can add another shim under the trans mount. That will raise the trans and allow me to drop the pinion the same amount. I think it will all work out OK though.
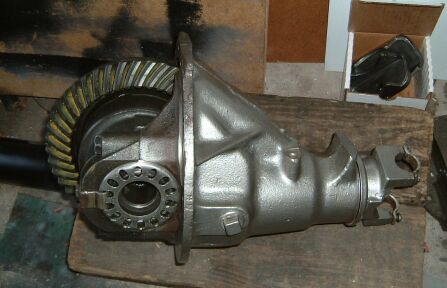
The next job was to remove the axle housing from the car and cut off the spring mounts so that I could set the pinion at the new angle on the new mounts you see in the photo.
I also fitted a drain plug at this stage.
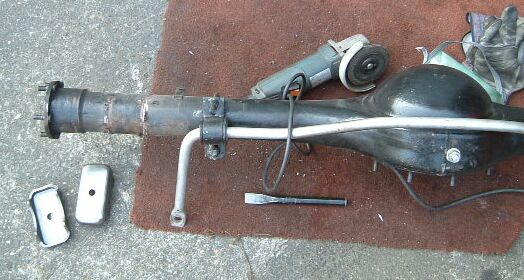
The brakes I left connected to save having to bleed them!
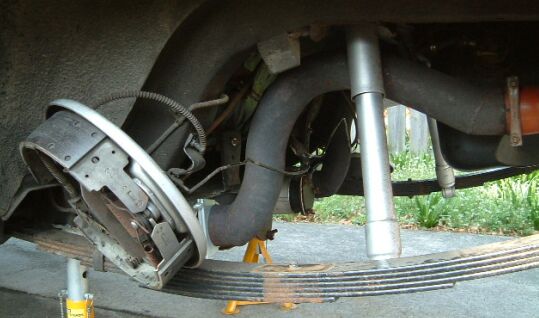
The axle was then re-fitted with the diff in place so that the pinion angle could be measured. But first the axle has to be centered under the car.
I did this first by measuring from the end of each axle to the springs.
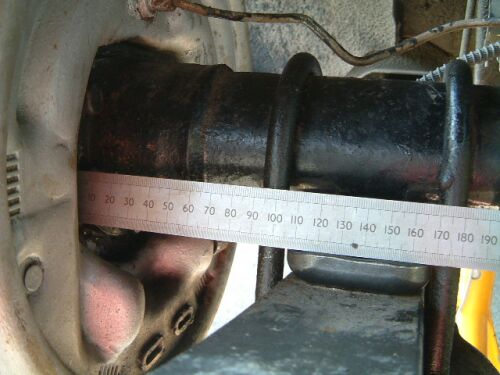
But then I found it was not centered under the body! (Well this is a Dodge!)
So I then set it so that it was right with the bodywork. There was only a couple of mm between the two measurements.
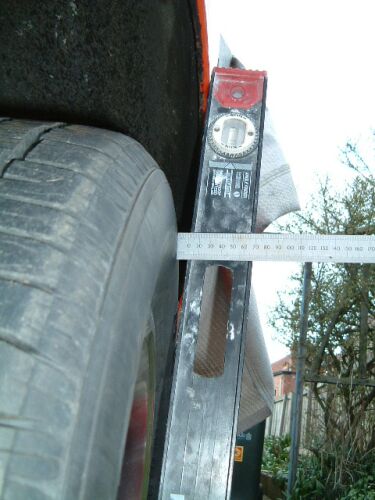
It was then just a matter of setting the pinion to the same angle as the engine/trans.
The theory goes like this;
The center line of the crankshaft and transmission output shaft must be parallel to the center line of the pinion shaft as shown in Figure 1.
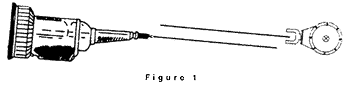
You will note that there is some distance between these parallel lines. The distance is caused by the angle of the components and their distance apart.
Planning these component angles is critical. You have to set the components up so their center lines are parallel and so that the angle made THROUGH the U-joints is 3-degrees or less as shown in Figure 2.
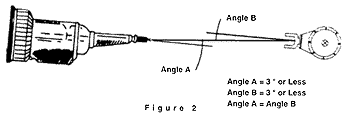
While it is possible to run at zero degrees through the U-joints, something more than one degree and less than three degrees seems to run smoothest.
This is something i got very wrong the last time I did it and the car has had a bad vibration since.
I will fit the driveshaft at the weekend and check all the angles again. I should have 1.5-2 degrees at the drivshaft when it is in. If I need more driveshaft angle I can add another shim under the trans mount. That will raise the trans and allow me to drop the pinion the same amount. I think it will all work out OK though.